Quality Liaison Services
Product Quality Monitoring
Services
If you’re a supplier of components or assemblies to an OEM, relationship management is central to sustaining your business. With many manufacturers vying for position with the customer, slip-ups like product nonconformance’s can make you fall out of favor.
Strengthen supplier-OEM trust with product quality monitoring from Quality Liaison Services. More than simply checking parts for accuracy, we’re in the facility on your behalf, advocating for you and learning how your performance and products are viewed from the OEM’s perspective. Our third-party OEM quality monitoring process insight is relayed instantly, enabling you to meet and exceed expectations.
Why Third-Party Product Quality Liaison Is Crucial?
For an OEM, receiving nonconforming parts isn’t a mere inconvenience; it’s a disruption. Such misalignments can halt production, causing missed targets and revenue losses
Consequently, suppliers may face penalties. In a market crowded with manufacturers, OEMs have the option to pivot. They might reduce orders from suppliers, neglect quality concerns, or even terminate the partnership. Such a scenario can be disastrous for suppliers, jeopardizing their entire business. It underscores the essential role third-party quality monitoring plays in ensuring consistency, trust, and sustainability in supplier-OEM relationships.
Generating Value
A Satisfied Supplier Customer?
“TMG’s quality management support system has been a game-changer for us. The communication aspect is truly commendable. I must especially mention Dot; their recent contributions have been impressive. They’ve truly taken their role to the next level.”
Reasons To Partner
With TMG:
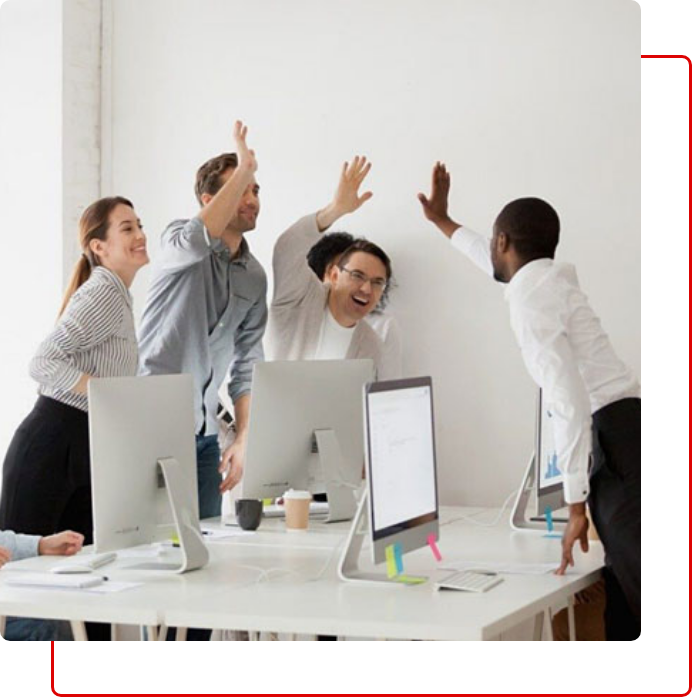
Solid Reputation:
Our credibility stems from our consistent excellence on the manufacturing floor.
Always Available:
With our 24/7 immediate response system, we’re always there when you need us.
Technical Expertise:
Our team is experienced and technically adept, ensuring the proper knowledge for every task.
Meticulous Approach:
We pride ourselves on our multifunctional attention to detail, ensuring nothing slips through the cracks
Cloud-Powered:
Our cloud-based project tracking system ensures transparency and real-time updates.
Plant-wide Recognition:
TMG boasts wide-ranging accessibility and recognition across plants, reflecting our established presence and trust in the industry.
Opt for TMG, and you’re choosing a partnership rooted in quality, dedication, and results.
More Visibility Means Better
Quality, Stronger Relationships
Third-party Quality Liaison Monitoring Process:
At TMG, we ensure suppliers are aware of unforeseen nonconformances, expensive penalties, or unexpected hits to their Key Performance Indicators. We have specialized representatives who actively monitor processes, acting as your advocates and swiftly relaying their findings. This means you can act promptly when it counts.
How Do We Do It?
On-site Presence:
We position our adept quality professionals at your customer’s facility. They inspect parts and closely observe activities.
Building Relationships:
Our team interacts with and understands the perspectives of installers, quality teams, engineers, and plant managers. More importantly, we gauge their perception of your products and services.
Real-time Feedback:
Leveraging cloud technology, our tracking software delivers immediate updates. You get exclusive access to a dashboard, presenting centralized project insights and live data, including inspection outcomes and potential areas for enhancement.
Seeking to Elevate Your Operational Excellence? Let TMG assist.
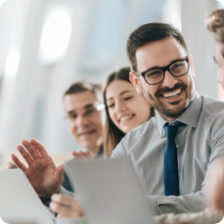
Boost Your Output
OEM Services
TMG bridges the gap between OEMs and their suppliers. We’re your dedicated point of contact, adeptly managing quality challenges, installation alterations, and specialized tasks.
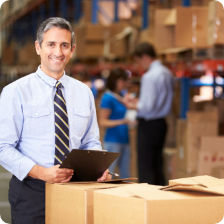
Enhance Your Client Bonds
Supplier Services
For suppliers, TMG is the go-to partner for swift resolutions. With a focus on unparalleled communication, we tackle diverse issues that arise in-house and within OEM client establishments.
Experience The TMG
Advantage
You invest in solution-driven representation when collaborating with TMG for third-party product monitoring. Our team arrives equipped with all the necessary personal protective gear and a professional attitude that echoes our commitment to quality. You can check our comprehensive list for a detailed inventory of items we include.
With TMG’s unparalleled third-party product quality monitoring, suppliers can sidestep hefty fines or disruptions in their component supply. Concurrently, OEMs benefit by evading high-priced warranty claims and potentially reputation-tainting issues. The culmination of this enhanced quality is a fortified bond between suppliers and their clientele.
Why Select TMG As Your Quality
Watchdog?
We spring into action only when you require monitoring at an OEM facility, making your urgencies and time constraints our top priority. We pridefully serve as the designated third-party product quality monitor for numerous sectors.
Our modus operandi strictly adheres to rigorous quality standards. Our readiness is unwavering – 24 hours a day, seven days a week, ensuring you’re always supported.
Are you considering launching a project? Let’s set it on the path to success. As pioneers in third-party product quality monitoring, we’re poised to champion your cause.
Delivering Excellence Through:
Comprehensive Plant-Wide Accessibility and Recognition.
In-depth Analytical Reports.
Immediate Responsive Actions.
Meticulous Attention to Nuances.
Rapid yet Accurate Inspections.
Swift Identification and Containment of Nonconformities.
On-Site Presence for Maximum Insight.
Industries We Serve Include.
HD Truck Assembly
Medical Devices
OEM Manufactures
Aerospace
Forging Facilities
We got you covered when you choose to do business with TMG.
Rework & Repair:
The Answer to Supply Chain Disruptions
Manufacturing imperfections are an inevitable challenge, but the ripple effects can be detrimental when faulty components reach the Original Equipment Manufacturer (OEM). It can hamper production goals, impede workforce productivity, and erode suppliers’ trust.
Yet, a batch of flawed products doesn’t spell catastrophe. With the Talent Management Group (TMG), you can bypass the repercussions of downtime and shipping delays. Our premium containment, repair, and rework services are tailored to safeguard the smooth flow of your operations.
Why Choose TMG’s Rework & Repair Services?
Experience & Expertise:
We pride ourselves on the seasoned expertise of our team. Their profound knowledge ensures that over 70% of the detected defective parts are rectified proficiently.
Economical Solutions:
Engaging with TMG means you can sidestep the financial strain of return shipping and the cost of replacement components
Enhanced Efficiency:
With our intervention, OEMs witness a drastic reduction in downtime, bolstering their productivity and delivery timelines.
Versatility:
Whether rejuvenating parts from your suppliers within your facility or managing your components at the OEM’s location, TMG has versatility and proficiency in delivering. Our reach spans North America, ensuring you always have a trusted partner nearby.
Seamless Operations With TMG
By choosing Talent Management Group, you’re not just opting for a service – you’re ensuring seamless operations, retaining supplier confidence, and fortifying the backbone of your manufacturing process. Reach out to TMG today to experience a world where rework and repair synchronize perfectly with your production goals.
The Power of Onsite Repair & Rework
Every product defect, no matter its nature or extent, threatens the integrity of suppliers and OEMs. Faulty components can dent a company’s finances and tarnish its reputation, leading to unsatisfied customers and a compromised brand image.
Yet, it’s not all doom and gloom. The silver lining lies in onsite repair and rework services – an efficient approach to nip quality concerns before they snowball into more significant issues.
Advantages of Onsite Rework & Repair:
Cost Efficiency:
Onsite services can lead to substantial long-term savings, avoiding the costs of larger-scale recalls or more intensive repairs.
Seamless Operations:
Keeping the work going without hiccups ensures a steady workflow, leading to timely deliveries and satisfied customers.
Optimized Productivity:
With minimal downtime for your employees, you ensure optimal productivity levels and reduced operational hiccups.
Economic Solutions:
Eliminate the costs and complexities of return shipping.
Uninterrupted Production:
Maintain the rhythm of your production flow, ensuring that every other downstream activity remains unaffected.
Risk Mitigation:
Proactively addressing issues head-on helps avoid potential penalties and legal ramifications associated with defective products.
For modern OEMs, bringing in expert support to manage these challenges means they can stay focused on their core competencies. Talent Management Group (TMG) is a trusted ally in this domain, ensuring product quality is never compromised.
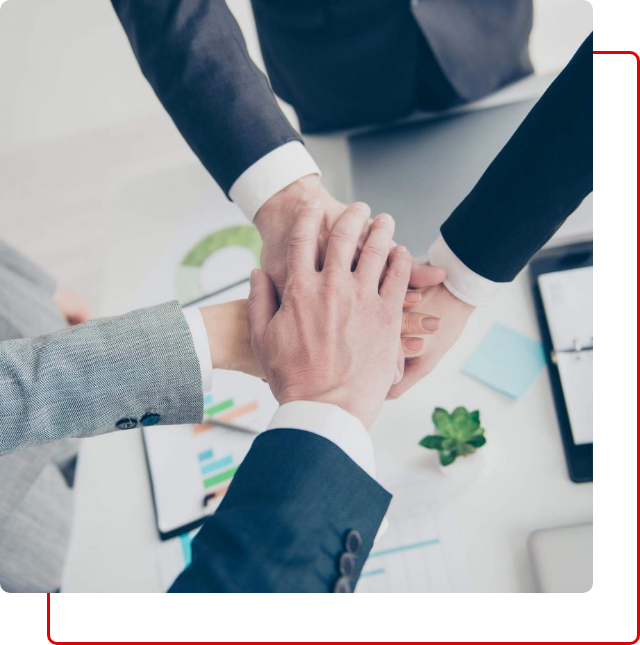
Choose Quality, Choose TMG
Elevate the standards of your operations and safeguard your brand’s reputation with TMG’s onsite repair and rework services. Ready for a seamless, defect-free production process? Talk to our experts now!
Harnessing The Proactive Approach Of TMG
In manufacturing, a proactive strategy can be the difference between streamlined operations and constant firefighting. Supplier testimonials speak volumes about an organization’s operational style, and for TMG, the message is clear.
According To A Valued Supplier-Customer:
“TMG has more of a plan and strategy put together when they come into the plant, whereas
other providers are followers and just wait to be told what to do.”
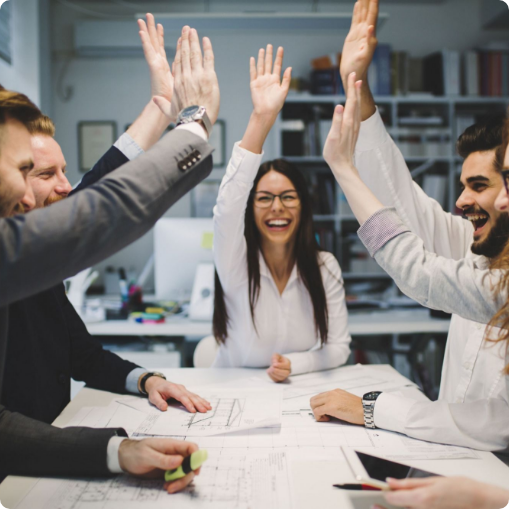
This feedback underscores TMG’s commitment to being a trailblazer rather than a mere participant. While many providers wait in the wings, TMG steps forward with a clear action plan. It’s not about merely responding to challenges but anticipating and mitigating them, ensuring smooth operations for all stakeholders involved.
TMG is the evident choice for businesses that seek not just a service provider but a strategic partner. The difference lies in the approach: Think ahead, act proactively, and create a roadmap for success.
Choose Talent Management Group — where foresight meets excellence.
Zeroing In On Productivity With TMG:
Production lines are the lifeblood of any manufacturing entity. The aim is straightforward: keep the lines moving and ensure that every product meets the desired standards. However, in the actual manufacturing world, there are inevitable hiccups — particularly when supply chain issues interrupt the rhythm.
But what if there was a way to focus solely on production and leave supply chain challenges in capable hands?
Enter TMG. Our commitment is to ensure that part conformance issues, a regular adversary in the manufacturing process, keep your productivity strong. Rather than reacting to problems as they arise, our onsite containment, rework, and repair services are structured to anticipate and address issues in their infancy.
With TMG, You Gain:
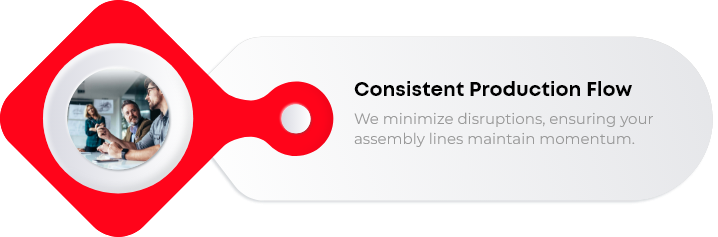
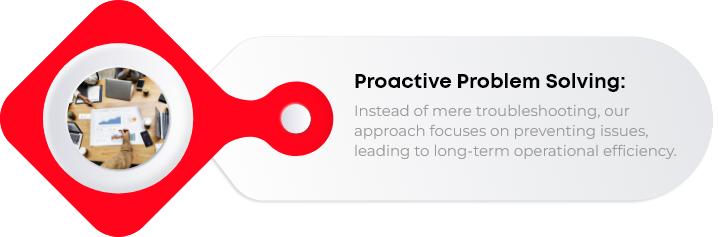
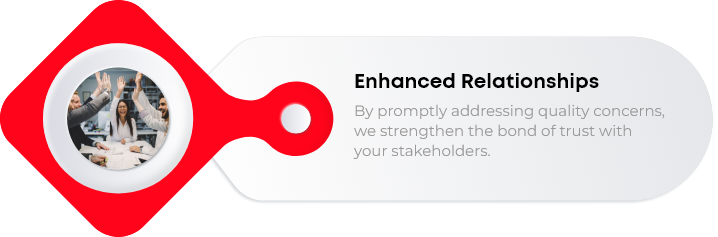
In a world where time equates to money, our solutions ensure that every second on your production floor counts. Stay ahead, stay productive, and let TMG handle the intricacies of supply chain quality assurance.
Focus on what you do best and let us manage the rest.